How India is pursuing self-sufficiency in the semicon chip value chain
Many countries are vying to build resilient semiconductor supply chains amid rising chip import prices
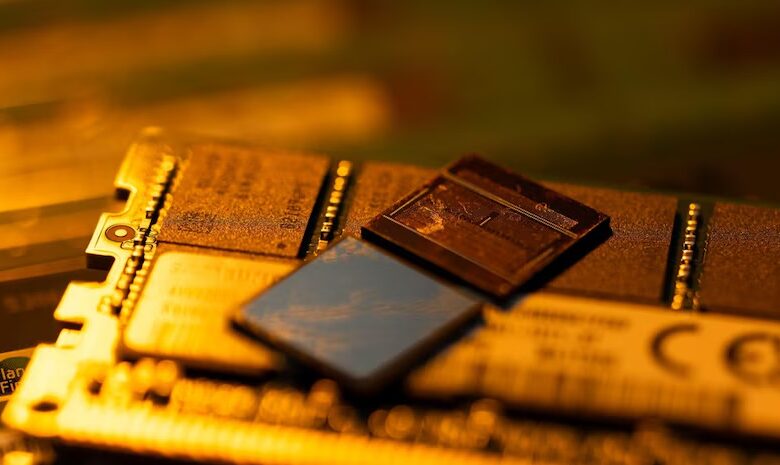
In September 2024, India and Singapore signed an MoU to partner and cooperate in semiconductors. Within a few weeks, India’s semiconductor chip manufacturing aspirations were bolstered by an agreement with the US to establish a joint semiconductor fabrication plant in India.
Many countries are vying to build resilient semiconductor supply chains amid rising chip import prices. PM Modi has long positioned India as a semiconductor hub alternative. He reiterated this in his recent pitch to chipmakers at India’s most recent SEMICON conference in 2024.
India Semiconductor Mission (ISM) has been a major government intervention to attract investments and incentivise local production. Launched in December 2021 with an outlay of Rs 76,000 crore, ISM offers production-linked and design-linked incentives for firms to establish semiconductor fabrication units, testing facilities, and design centres within India. The initiative has already pulled in Rs 1.5 trillion in investments from major players like Micron, Tata Electronics, CG Power, and Kaynes Technology.
The question, however, remains: Can India increase its semiconductor self-sufficiency and become a key player in global semiconductor value chains with this Rs 76,000 crore chip bet and global partnerships?
Revealed competitive advantage in chip design
The semiconductor value chain encompasses four key stages – design, manufacturing, ATP – assembly, testing and packaging, and distribution. With talent requirements more important than capital, the chip design stage is perhaps where India has already established capabilities. India is home to 20 per cent of the global talent pool for chip design, primarily employed by MNC subsidiaries in India. Global chipmaker AMD recently opened its largest global design centre in Bengaluru.
India’s domestic design capabilities are also due to expand – driven by the design-linked incentives from ISM that specifically target domestic design firms. To meet the growing demand for design talent, the government is equipping over 100 colleges with electronic design automation tools from Siemens, Synopsys, and Cadence.
Techno-nationalism: From fabless to fab
Although India’s current capabilities favour specialising in “fabless” chip design firms, the recent slew of government approvals indicate efforts at building domestic chipmaking factories known as “fabs”. The Dholera plant, launched by Taiwan’s PSMC and Tata Electronics in March 2024, marks India’s first semiconductor fab in 30 years. The government funds 70 per cent of the investment, with Tata Group covering the rest and PSMC overseeing technology transfer and employee training.
Despite being a “late” latecomer in the semiconductor fabs bandwagon, as noted in a 2023 WTO report, India is trying to leverage the recent supply chain reconfiguration to its advantage. During the 2018-2023 period, 80 per cent of the fabrication stage in semiconductors was concentrated in Taiwan, South Korea, People’s Republic of China, Japan and Singapore. The Covid-19 pandemic and the rising geopolitical tensions make the East Asia concentration a vulnerability to many countries, according to the 2023 WTO report – India aspires to be a viable alternative.
Developing a fab ecosystem is not without challenges. The first is the more obvious one – the enormous costs of building new fabs. In 1983, constructing a bleeding-edge semiconductor fab cost about $200 million. By the early 2020s, that price tag soared to well over $20 billion, with operational expenses over the next decade matching the hefty initial investment. The huge investments required for the “fab model” seem to be a risky bet for India as the prospect of achieving technological sovereignty in semiconductor fabs cannot be guaranteed.
Another hurdle is the extremely resource-intensive nature of the fabrication process, requiring a steady power supply and vast amounts of “ultrapure water” to clean silicon chips. A typical facility today can consume up to 10 million gallons of ultrapure water daily. The thirsty fabs could put more pressure on India’s already stressed water systems, and the power supply demand could impede the national mandates on net-zero targets.
The talent and skills gap as the fab model expands is also a concern. The 2022 National Skill Development Corporation (NSDC) report finds the supply of skilled workers needed to operate the semiconductor manufacturing plants falling short of the demand. Another report by TeamLease Degree Apprenticeship projects India to encounter a shortage of 250,000 to 300,000 professionals in the semiconductor industry by 2027.
A more crucial and basic bottleneck to India’s fab aspirations is its over-reliance on imports, particularly from China, for critical minerals essential for chip manufacturing, including Rare Earth Elements (REEs). Despite holding 6 per cent of global REE reserves, mining efforts have been non-existent since the 1950s, and India has only utilised 10-20 per cent of its exploration capacity for critical minerals.
A quick win through assembly capabilities?
India could adopt a quicker, more feasible semiconductor strategy by focusing on the back-end manufacturing stage of ATP. This stage transforms silicon wafers from front-end fabs into finished chips ready for electronic devices. Specialist firms handle tasks like slicing, packaging, and testing, then ship the chips to manufacturers. ATP is a relatively easier segment to enter for India, thanks to lesser capital but more labour-intensive requirements than front-end production.
MNCs set up ATP facilities to a larger extent in developing countries. As Chris Miller, author of Chip Wars, noted, Korea, Taiwan, and Singapore initially entered the chip industry through assembly, testing, and packaging before advancing to fabrication. Therefore, a near-term focus of India’s semiconductor industrial strategy could lie in developing ATP capabilities.
India has already recognised the potential of the ATP segment. After the Micron assembly plant approval, the government recently approved Tata’s Rs 27,000 crore investment for a greenfield facility in Assam that will focus on the assembly and testing of semiconductor chips. Suchi Semicon also recently announced a $100 million investment in Gujarat’s first Outsourced Semiconductor Assembly and Testing plant, set to begin semiconductor rollout this November.
Electronics manufacturers that have shifted production to India are already taking advantage of this ATP focus. Apple, for instance, is in talks with Micron, the Tata Group, and other chip manufacturers establishing facilities in India to source $12 billion worth of components for its devices.
Value chain self-reliance a distant dream
India’s ambition to master all stages of the semiconductor value chain is neither easy, nor credible. Semiconductor value chains are highly complex, far beyond the scope anticipated by “self-sufficiency” policy advocates. A practical path forward includes indigenising India’s strength in fabless design and expanding ATP facilities, while also venturing into semiconductor fabrication to reduce dependency on imports and meet India’s vast demand for electronic products. With chips crossing around 70 borders before reaching end users, India cannot navigate this journey alone. Strategic global partnerships, like those established with Singapore and the US, will be essential for India to become a powerhouse in the semiconductor value chain.
Source: BusinessStandard