Ferrari unveils F80, its most powerful supercar to date
The F80 is Ferrari’s new supercar, a car destined to join iconic models from the 1984 GTO to the 2016 LaFerrari Aperta
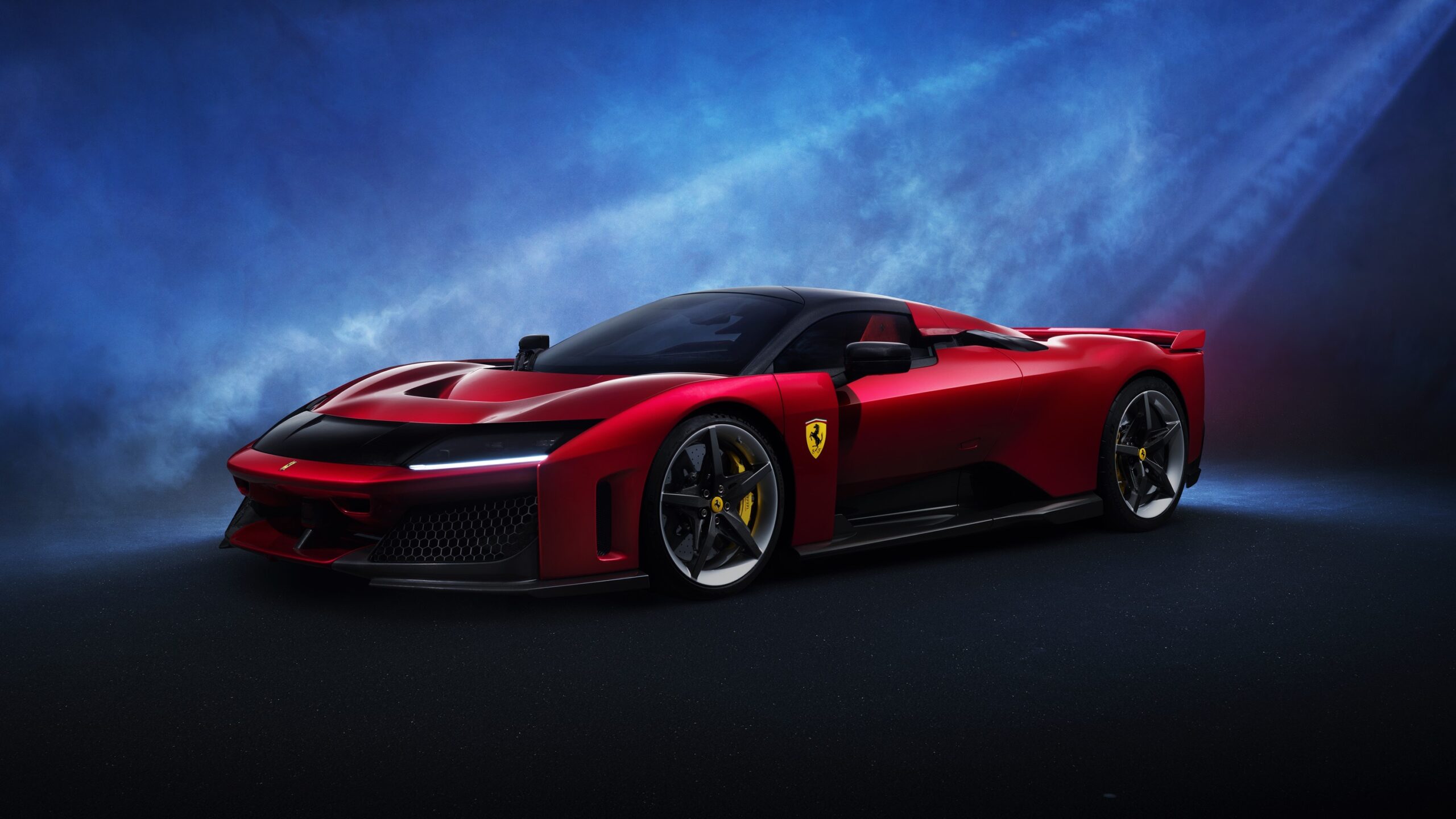
• The F80 is a showcase for the ultimate in technology and performance from the marque, and represents an extreme development of the internal combustion engine
• With a combined maximum power of 1200 hp, the V6-hybrid powertrain of the F80 makes it the most powerful road car ever to come out of the gates of the Ferrari factory
• A host of advanced technological solutions makes the F80 the new benchmark for innovation and engineering excellence
Ferrari today unveiled the F80 and wrote a new chapter in the history of legendary supercars bearing the Prancing Horse badge. The F80 will be produced in a limited run of just 799 examples and joins the pantheon of icons such as the GTO, F40 and LaFerrari by showcasing the best that the Maranello-based marque has achieved in terms of technology and performance.
Ever since 1984, Ferrari has periodically released a new supercar that represented the pinnacle of cutting-edge technology and innovation of its era and that was destined to become enshrined in popular culture. Intended for the most discerning clients of the brand, these cars immediately became legends in their own lifetime, making an indelible mark not only on the history of Ferrari, but on the history of the automobile itself.
The latest addition to this family, the F80, is tasked with embodying the ultimate in engineering for an internal-combustion-engined vehicle and employs all the most advanced technological solutions, including latest-generation hybrid technology for the powertrain, to achieve unparalleled levels of power and torque. Every aspect of the architecture is conceived to maximise performance, from the carbon-fibre chassis and extreme aerodynamic solutions far beyond anything seen before in a roadlegal car, to the new active suspension optimised to let the driver wring every ounce of performance from the car on the track.
Unlike anything else in the current supercar world, the F80 combines all these attributes with uncompromising levels of usability on the road, where it can be driven with ease. This ability shaped every choice made in terms of technology and architecture to achieve the goal, which at first sight seems impossible, of creating a track-oriented supercar that’s just as driveable as a production range model.
All this means that the driver will spend even more time in the car and can truly get to know and revel in its performance and the thrilling driving experience it offers. The architecture of the F80 is so extreme that the layout chosen results in a narrower cabin with a driver-centric layout, which nonetheless still offers excellent space and comfort for a passenger. This choice had crucial benefits in terms of minimising drag and weight.
The cockpit area therefore has a distinct single-seater feel, despite the fact that the car is homologated for two occupants, resulting in a architecture that we could call “1+”. The primary reason for this choice was to minimise width, to the benefit of aerodynamics (with less drag) and weight saving. This concept is completely in keeping with the motorsport world from which this car not only draws inspiration but also inherits technological solutions.
As has always been the case with the Ferrari supercars preceding the F80, the powertrain is based on the finest expression of technology in motorsport. The GTO and F40 were powered by a turbo V8, because Formula 1 cars used turbocharged engines in the 1980s. Today in both Formula 1 and the World Endurance Championship (WEC), powertrains consist of turbo V6 ICE engines mated with an 800 V hybrid system. It was only natural then that this architecture – the same architecture used by the 499P, which has taken two consecutive victories at the 24 Hours of Le Mans – would be transferred into the new F80.
Here though the powertrain is further complemented by the introduction, for the first time ever on a Ferrari, of electric turbo technology (e-turbo), which, with an electric motor installed between the turbine and compressor of each turbo, allows for an extraordinary specific power output and instantaneous response from low down in the rev range.
Aerodynamics play a key role on the F80, with solutions such as the active rear wing, rear diffuser, flat underbody, front triplane wing and S-Duct working in concert to generate 1000 kg of downforce at 250 km/h. This result is further enhanced thanks to the active suspension, which contributes directly to generating ground effect. Performance is boosted by the electric front axle, which brings fourwheel drive capability to make even more effective use of the torque and power on tap, and the new brakes with motorsports-derived CCM-R Plus technology.
As with all the supercars preceding it, the F80 marks the start of a new design era for Ferrari, with a more tense, extreme design language accentuating its race-bred soul. There are clear references to cues borrowed from aerospace, which underscore the cutting-edge technology and elegant engineering of each and every technical solution. But there are also nods to its hallowed progenitors which clearly declare the illustrious lineage of the F80.
Power train
Internal combustion engine
The three-litre 120° V6 F163CF of the F80 is the ultimate expression of the Ferrari six cylinder engine: this unit produces an astonishing peak power of 900 hp, making it the Ferrari engine with the highest specific power of all time (300 cv/l), to which the electric front axle (e-4WD) and rear motor (MGU-K) of the hybrid system add another 300 cv.
The link with motorsports, and endurance racing in particular, is strong: the architecture of this engine and many of its components are closely derived from the powerplant of the 499P which won the last two editions of the 24 Hours of Le Mans. Commonalities with the car competing in the World Endurance Championship (WEC) include the architecture, crankcase, layout and drive chains of the timing system, oil pump recovery circuit, bearings, injectors and GDI pumps.
Naturally, there is also technology carried over from Formula 1, from which the F80 inherits both the concept of the MGU-K (with the development of an industrially manufacturable electric motor similar to the unit used in Ferrari F1 cars) and the MGU-Hs (which generate power from the excess kinetic energy from the rotation of the turbines created by the heat energy from the exhaust gases) with a bespoke e-turbo application.
For maximum performance in all possible conditions, every aspect of the calibration of the engine has been taken to the extreme, focusing in particular on the ignition and injection timing, the number of injection events per stroke and the management of the variable-phase valve timing. The F80 is equipped with the first Ferrari road car engine to benefit from a new approach for statistical knock control, which lets the engine operate even closer to the knock limit, allowing the use of higher combustion chamber pressures than ever (+20% compared with the 296 GTB) to unleash even more of the engine’s potential.
Another crucial aspect has been the work dedicated to the dynamic calibration of the torque curve in every gear, an all-time first for a Ferrari road car. This part of the project focused on real road-driving conditions and the management of the e-turbo system, because knock and compressor surge limits vary depending on whether they are measured in dynamic or stationary conditions. As a result of this research, a dedicated calibration was developed for each gear, allowing the engine to attain levels of responsiveness comparable to a naturally-aspirated engine in all operating conditions.
The e-turbos, with an electric motor installed axially between the turbine and the compressor housing, let the engineers optimise the fluid dynamics of the engine for maximum power at mid to high engine speeds without the usual compromise this entails in terms of turbo lag at low engine speeds. Bringing electric power into the equation makes it possible to define e-turbo management strategies which negate turbo lag and ensure lightning-quick response times.
The 350 bar injectors of the GDI system are situated at the centre of the combustion chamber for optimal fuel/air mixing and, together with the multiple injection strategies adopted, ensure efficiency for outstanding performance with lower emissions. The intake and exhaust cam profiles have been revised to optimise fluid dynamic efficiency and increase maximum engine speed to 9000 rpm, with a dynamic limiter at 9200 rpm.
Both the intake and exhaust runners are polished for better performance; the intake runners have been shortened to reduce resistance and cool the air/fuel mixture through fluid dynamic detuning, and are specifically designed to increase turbulence in the combustion chamber. The three-brick (matrices) exhaust line complies with current emissions standards (Euro 6E-bis), but already takes future evolutions in emissions regulations on a global level into account.
The Inconel© exhaust manifolds are designed to minimise pressure losses and are tuned to emphasise the distinctive sound of a Ferrari V6. The steel crankshaft is machined from a die-cast element and features hot-forged crankpins with an offset angle of 120°. The 1-6-3-4-2-5 firing order lends the F80 a typical Ferrari timbre. To reduce weight, the crankshaft webs and counterweights have been lightened.
The connecting rods and pistons have also been revised: the titanium connecting rods feature a toothed interface at the mating surface between the shank and the big end cap to ensure perfect alignment between the two parts and absolute assembly precision with the bearings. The aluminium pistons have been optimised to reduce weight and withstand the higher pressure and thermal loads in the combustion chamber due to the incredibly high torque and power. Specifically, high strength DCL (diamond-like carbon) coated steel has been used for the piston pin. Additionally, a dedicated oil passage hole has been added to the zone between the piston pin and the connecting rod to improve lubrication.
To lower the centre of gravity of the car, the engine has been installed as close as physically possible to the flat undertray. As a result, none of the components situated at the bottom of the sump are more than 100 mm below the centreline of the crankshaft. It was also decided to tilt the engine-transmission unit by 1.3° in the Z axis, raising the gearbox so that it does not compromise the efficacy of the aerodynamic undertray.
To lighten the engine, the cylinder block, crankcase, timing cover and other components have been revised, while titanium screws have also been adopted. As a result of these measures, the engine weighs no more than the V6 of the 296 GTB despite a power increase of 237 hp.
The lowered installation position of the engine-transmission unit was permitted by the new smaller diameter flywheel, conceived and designed from scratch for this application. This innovative solution was made possible by the use of two sets of springs, which also contributed to reducing the overall stiffness of the system and filtering vibrations transferred to the transmission more effectively. The damper was also developed specifically for this application to attenuate the higher torsional vibration forces in the driveline and dissipate the higher thermal loads due to the increased performance.
Hybrid Power train
The electric motors used for the F80 are the first units developed, tested and manufactured entirely by Ferrari at Maranello, all with the specific goal of maximising performance and reducing weight. Their design (with two on the front axle and one at the rear of the car) draws directly from Ferrari’s experience in racing; specifically, the stator and rotor in a Halbach array configuration (which uses a special layout of the magnets to maximisemagnetic field strength) and magnet sleeve in carbon fibre are all solutions derived from the design of the MGU-K unit used in Formula 1.
The rotor adopts Halbach array technology to maximise magnetic flux density and minimise weight and inertia. The carbon fibre magnet sleeve, on the other hand, has been used to raise maximum motor speed to 30,000 rpm. The concentrated winding stator reduces the weight of copper used for the end windings, while the Litz wire minimiseshigh-frequency losses. The Litz consists of multiple insulated strands instead of a single wire, reducing the ‘skin effect’ and allowing the current to flow uniformly through the entire cross section of the wire to minimise losses. The resin coating for all the active parts of the stator improves heat dissipation.
A DC/DC converter transforms DC current at one voltage to DC current at a different voltage. This innovative technology makes it possible to use a single component to handle three different voltages simultaneously: 800 V, 48 V and 12 V.
Using the direct current produced by the high-voltage battery at 800 V, the Ferrari converter generates direct current at 48 V to power the active suspension and e-turbo systems, and 12 V direct current to power the electronic control units and all other electric ancillaries on the vehicle. Innovative resonant technology allows this component to convert current with no latency with a conversion efficiency in excess of 98%, so that it behaves to all intents and purposes as an accumulator. This component eliminated the need for a 48 V battery, saving weight and simplifying the layout of the electrical system.
Also developed and manufactured entirely in-house by Ferrari, the front axle includes two electric motors, an inverter and an integrated cooling system. This component makes it possible to use torque vectoring for the front axle. Integrating different functions in a single component and the new mechanical layout have offered a weight saving of around 14 kg over previous applications, and the entire component weighs just 61.5 kg. Optimising mechanical efficiency was a primary goal: low viscosity oil (Shell E6+) and a dry sump active lubrication system with an oil tank integrated directly into the axle reduced mechanical power losses by 20%. The use of high coverage ratio (HCR) gears contributed to reducing noise emissions by 10 dB.
The direct current received from the high-voltage battery is transformed into the alternating current necessary to power the electric motor by the inverter. The inverter integrated in the front axle is bidirectional, meaning that it also transforms alternating current produced by the axle under regenerative braking into direct current for recharging the battery. The inverter used to convert power and control the two front motors is capable of delivering a total of 210 kW of power to the axle. On the F80, the inverter is integrated directly into the axle and weighs just 9 kg, contributing to the lower mass of this component compared to its counterpart on the SF90 Stradale.
Another inverter is used for the rear electric motor (MGU-K). This performs three functions: starting the internal combustion engine, recovering energy to recharge the high voltage battery and supplementing the torque of the engine in certain dynamic conditions. It can generate up to 70 kW in regeneration mode and assist the internal combustion engine with up to 60 kW of power. Integrated into both of these inverters is the Ferrari Power Pack (FPP) system, a power module with all the elements necessary for power conversion combined in the most compact unit possible. This unit consists of six modules in silicon carbide (SiC), gate driver boards and a dedicated cooling system.
The core of the energy accumulation system – the high-voltage battery – is conceived for very high power density. The innovative design of the battery is based on three principles: lithium-cell chemistry derived from Formula 1, an extensive use of carbon fibre for the construction of the monocoque casing, and a patented design and assembly method (cell-to-pack) which minimises the weight and volume of the unit. Situated low down in the engine bay, the pack contributes to even better dynamic vehicle behaviour by lowering the car’s centre of gravity. All electrical and hydraulic circuit connectors are built into the component to reduce cable and hose length, while the pack is configured with 204 cells connected in series and subdivided equally into 3 modules, for a total energy capacity of 2.3 kWh and a maximum power output of 242 kW.
Last but not least, to improve integration between the electric and electronic internal components, Ferrari developed the CSC (Cell Sensing Circuit) wireless sensor suite, which monitors cell voltage with spring contacts and measures cell temperatures with infrared sensors.
Aerodynamics
The F80 pushes aerodynamic performance to levels never seen before on a Ferrari roadcar, as testified by the 1000 kg of downforce produced at 250 km/h. This astonishing achievement was made possible by perfect symbiosis between all the internal Ferrari departments working on the definition of the car’s architecture; for each department, the perfect balance between downforce and top speed was the basis for every design choice, giving shape to a suite of extreme solutions befitting a true supercar.
The front end of the F80, which develops 460 kg of total downforce at 250 km/h, was inspired by the aerodynamic concepts employed in Formula 1 and the World Endurance Championship (WEC), innovatively reinterpreted for this application to become cornerstones of the entire design. On the one hand, the recumbent racing driving position allowed for a chassis with a high centre keel, while on the other, the cooling system layout has freed up the entire central portion of the vehicle, maximising the space usable for other functions.
The body-coloured central volume of the nose acts as the generously-sized main plane of the front wing. Inside the S-Duct are two flaps following the main profile to complete the triplane wing configuration with curvatures and blower slots clearly inspired by the 499P. Crucial for the aerodynamic efficacy of the front of the vehicle is the way the triplane works in perfect concert with the S-Duct and the high central keel, minimising blockage of the air flow towards the wing and maximising performance.
As a result, the air flow from the underbody and bumper undergoes violent vertical expansion and is redirected within the duct towards the front bonnet, generating a potent upwash which translates into a powerful low-pressure zone under the underbody. This accounts for 150 of the 460 kg of the maximum downforce generated at the front of the car which, however, is very sensitive to changes in ground clearance. The aerodynamic balance of the car is therefore ensured by the active suspension, which controls the attitude of the vehicle in real time and adjusts the distance between the underbody and the road in response to driving conditions.
The volume freed up under the feet of the driver also made room for three pairs of bargeboards. These devices generate powerful, concentrated vortices which introduce a velocity component to the airflow field in the outwash direction. In addition to improving the underbody’s suction, the outwash also reduces blockage and improves the performance of the front triplane. The bargeboards also help mitigate the detrimental effects of the wake of the front wheel by confining it and keeping it away from the undertbody, preventing contamination of the air flow directed to the rear of the car.
The aerodynamic performance of the rear zone of the car, which generates the remaining 590 kg of downforce at 250 km/h, is a result of the combined action of the rear wing-diffuser system. The efficiency of this system is highly dependent on the quantity of downforce produced by the underbody, as this has very little impact on drag.
To take the performance of the diffuser of the F80 to extreme levels, the expansion volume of the diffuser itself has been maximised by inclining the engine-gearbox unit by 1.3° in the Z axis, and by the configuration of the rear chassis and suspension components. The starting point of the upward curvature of the diffuser has been brought forward, resulting in a diffuser measuring a recordbreaking 1800 mm in length, which generates a huge low-pressure zone underneath the vehicle, which in turn draws a massive flow of air into the underbody area.
The geometry of the chassis, with narrow, curved sills, contributes to creating an aerodynamic seal effect around the underbody by forming a duct that captures the flow adhering to the flank and blows air into the interior of the rear wheelarch housing under the lower suspension arm. The interaction between this air flow and the outer strake of the diffuser interferes with the vortices generated in the wheel-road contact zone, preventing air from entering the diffuser too far forwards. These solutions work in such perfect harmony that the downforce generated by the diffuser alone is 285 kg, or more than 50% of the total downforce on the rear axle.
The active wing is the most visually distinctive aero feature of the F80, which completes the entire aerodynamic concept of the vehicle. The actuator system of the rear wing adjusts not only its height but also controls angle of attack continuously and dynamically, for precisely modulable downforce and drag. In the High Downforce (HD) configuration, which is used during braking, turn-in and cornering, the wing assumes an angle of 11° relative to the direction of the air flow to generate over 180 kg of downforce at 250 km/h.
At the extreme opposite of its range of rotation, the wing is in Low Drag (LD) configuration, with the leading edge pitched upwards. Drag is much lower in this configuration, not only because of the reduction in lift, but also due to the tractive effect generated by the residual low-pressure zone impinging on the underside of the wing itself.
The rear wing is the keystone of the entire adaptive aero system, allowing the F80 to adapt to any possible dynamic conditions, which are monitored and evaluated in real time by the vehicle control systems. In response to the requests of the driver in terms of acceleration, speed and steering angle, the system determines the optimal blend of downforce, aerodynamic balance and drag, and tells the active suspension and active aero systems to implement the ideal attitude accordingly. In the case of the aero system, this means controlling the angle of attack of the rear wing and the activation state of the Active Reverse Gurney flap under the front triplane.
With its two different configurations, the flap also allows control over downforce and drag at the front of the car: the closed position generates maximum downforce, while in the open position the device is at right angles to the air flow and, similarly to how DRS systems work in Formula 1, stalls the underbody to reduce drag and let the car reach a higher top speed.
Heat management
Defining the layout of the cooling system demanded in-depth studies and painstaking development to reconcile the thermal needs of the engine (which has to dissipate over 200 kW of thermal power during performance usage) and the new hybrid system with aerodynamic requisites. The aim was to design a cooling system with the least possible impact on the overall packaging, to attain a functionally and aerodynamically valid configuration that perfectly accommodates both the aerodynamic and thermal demands of the F80.
The radiators are positioned optimally to maximise the flow of cold air and minimiseinterference with the hot air flow, for better thermal exchange efficiency. A number ofother innovative solutions were also adopted to improve the overall thermal balance of the car, such as the transparent film embedded in the windscreen which uses power from the 48V circuit to demist the screen and reduce the power demand on the HVAC system. Additionally, the climate control circuit is controlled by electrically actuated valves which modulate the flow of refrigerant in relation to the needs of the HVB circuit, improving energy management.
At the front are two condensers serving the climate control, battery and active suspension circuit, plus three high temperature radiators for cooling the V6. Two of these are situated laterally, in outboard positions, to make the most effective use possible of the space between the underfloor and the headlights, while the third is situated at the centre and takes advantage of the upwash generated by the triplane to ensure adequate air flow.
The venting of the hot air flows has been optimised to not interfere with the front aerodynamics and the flows of cooling air directed towards the rear. The main vent of the lateral radiators opens inside the wheelarch housing, a solution offering the least possible blockage to ensure excellent permeability for the radiating masses. Another aperture in the flank of the front wing ahead of the wheel contributes to containing the wheel wake while also directing hot air around the exterior of the wheel. The centre radiator vents heat into the zone between the bumper and the front bonnet without interfering with the flow exiting the S-Duct.
A number of different functions are integrated into the flank of the F80 in a single formal solution described by the upper volume of the door, where the surface drops away gradually to give shape to a channel incorporated in the bodywork itself. The shape of this channel protects the air flow along the wing from thermal contamination by the hot wake of the front wheel and guides it along the surface of the door to the inlet at the leading edge of the flank. This air intake is topped by a winglet that reinterprets the distinctive form of NACA aeronautical inlets: a solution that exploits the vorticity of the air to capture part of the air stream flowing in the region above the duct. Inside the duct, the incoming air is split into two flows, with one feeding the induction system of the engine, which benefits from up to 5 hp of extra power as a result of ram effect, and the other feeding the intercooler, which cools the intake air, and the rear brakes.
Here too, the engineers opted for innovative solutions to keep the braking system – developed around state-of-the-art CCM-R Plus discs – working in optimal thermal conditions. These include a front duct that uses the hollow inner cavities of the front impact-absorbing chassis longerons to channel the highenergy cold air flow from the bumper to the discs, pads and callipers, which are the most sensitive elements of the system. For the first time ever, this solution, patented by Ferrari, turns what was a packaging constraint into a means to maximise cooling performance, and offers a 20% increase in cooling air flow compared the LaFerrari with no penalty in terms of front aerodynamics.
Vehicle dynamics
The F80 is equipped with the most advanced suite of technological solutions currently available for managing vehicle dynamics in all possible conditions on the road or track. The Ferrari active suspension system is undoubtedly one of the showpieces of these and has been re-engineered from the ground up compared with the version used on the Ferrari Purosangue to tailor it to the F80’s supercar soul.
The system features completely independent suspension all round actuated by four 48V electric motors, a double wishbone layout, active inboard dampers and upper wishbones created with 3D printing and additive manufacturing technology, which is used here for the first time on a Ferrari road car. This solution offers a number of advantages, such as an optimised layout, more precise wheel control, reduced unsprung mass, no requirement for an anti-roll bar and the introduction of a dedicated camber angle correction function.
This system fulfils two apparently irreconcilable requirements – the need for a very flat ride on the track, where variations in ride height must be minimised as much as possible, and the need for the compliance to effectively soak up bumps in road surfaces during normal driving. This means that the car boasts outstanding driveability on the road and can also manage downforce optimally in all possible conditions.
At low speeds, the system prioritises mechanical balance and centre of gravity control, while with increasing speed, the ride height control system works to optimise aerodynamic balance in each different cornering state in concert with the active aero system. When under hard braking, such as when entering a bend, ride height control minimises variations to prevent instability caused by the weight transfer towards the front that would usually occur in this scenario. While cornering, the system contributes to increasing downforce to maintain the optimal balance. As the car exits the bend, the system contrasts the tendency for the balance to shift towards the rear, maintaining the best possible conditions for traction for all four wheels and stability.
Another major evolution introduced by the F80 is the new SSC 9.0 (Side Slip Control) system, which now benefits from the integrated FIVE (Ferrari Integrated Vehicle Estimator) function. The new estimator is based on the concept of the digital twin, a mathematical model that uses the parameters acquired by sensors installed on the car to replicate its behaviour virtually.
As well as estimating yaw angle in real time, which was already possible with the previous generation, the new system also estimates the velocity of the centre of mass of the car, calculating each with a precision of under 1° and 1 km/h respectively. The new estimator improves the performance of all the dynamic control systems on board the vehicle, including traction control, for example.
Featuring the eManettino like all PHEV Ferrari models, the hybrid powertrain of the F80 offers three different driving modes: ‘Hybrid’, ‘Performance’ and ‘Qualify’. There is no eDrive mode, which is available on the SF90 Stradale and 296 GTB, because the F80 cannot be driven in full-electric mode, considered not be in keeping with the car’s mission.
‘Hybrid’ mode is selected by default when the vehicle is switched on and enables all the functions intended to make the vehicle more efficient and useable in all real-world conditions. This mode prioritises energy recovery and battery charge maintenance to prolong the ability of the MGU-K motor to deliver boost when needed. ‘Performance’ mode is geared towards delivering continuous levels of performance during extended stints on the track, optimising energy flows towards the battery to always keep a battery state of charge of around 70%. The most extreme performance mode, ‘Qualify’, lets the driver unleash all the power that the F80 has at its disposal, using electronic torque shaping during upshifts at the rev limiter to use the torque curves of the electric motor and ICE engine in the best combination possible for maximum performance.
‘Performance’ and ‘Qualify’ eManettino modes also offer the driver access to an all-new function marking a first not only for Ferrari but for the automotive industry as a whole: Boost Optimization, a technology that records the track where the vehicle is driving and delivers an extra power boost in the sections of the circuit where it is most needed. After selecting this function, the driver first drives around the track in a reconnaissance lap, during which the system identifies the curves and straights of the circuit, acquiring the data it needs to optimise power delivery. Once this lap is complete, the vehicle is ready to deliver the extra power needed automatically with no further action from the driver. How Boost Optimization is implemented depends on whether it is used in ‘Performance’ mode – where it maintains constantly available performance for as long as possible – or ‘Qualify’ mode, where it maximises the boost zones, even at the cost of a drop in high-voltage battery charge.
The braking system of the F80 introduces another important innovation: CCM-R Plus technology, developed in collaboration with Brembo. The adoption of materials and technologies derived directly from Ferrari’s experience in motorsports has given shape to a product with distinctly superior performance to any other road-going carbon ceramic system.
CCM-R Plus uses longer carbon fibres to significantly improve mechanical strength (+100%) and thermal conductivity (+300%) over the previous-generation solution. The braking surfaces are coated with layer of silicon carbide (SiC), which offers incredible wear resistance while also reducing beddingin times. These discs work in conjunction with brake pads with a specific new compound that ensures an extraordinarily constant coefficient of friction even during prolonged extreme usage on the circuit. The larger heat exchange area of the two rows of ventilation channels of the disc and their geometry, derived from F1 applications and optimised with advanced computational fluid dynamic (CFD) methods, ensure superior cooling.
Two tyre choices, with Pilot Sport Cup2 and Pilot Sport Cup2R variants, both offered in the sizes 285/30 R20 and 345/30 R21 (front/rear), were co-developed with Michelin for the F80. Pilot Sport Cup2 tyres feature a casing and tread designed specifically to offer a thrilling driving experience and maximise the usability of the car, while the Pilot Sport Cup2R uses specific compounds derived from motorsports applications to allow the car to reach previously unimaginable levels of performance on the track for a Ferrari road car in terms of both maximum grip and consistency over time.
And to maximise day to day usability, even when not driven at the limit, the F80 is equipped as standard with all the main ADAS driver assist functions currently available: Adaptive Cruise Control with Stop&Go function; Automatic Emergency Brake; Lane Departure Warning; Lane Keeping Assist; Automatic High Beam; Traffic Sign Recognition; and Driver Drowsiness and Attention Warning.
Chassis and bodyshell
Chassis
The tub and other elements of the chassis of the F80 were developed using a multi-material approach, where the best suited material for the task is used for each individual zone. The cell and roof are made of carbon fibre and other composites, while the front and rear subframes are made of aluminium and are fastened to the tub with titanium screws. At the rear there is an additional aluminium subframe, fastened to the main rear subframe with screws, for carrying the battery.
The subframes are made up of closed-end extrusions connected to each other by cast elements. The tub features hollow sills in carbon fibre serving as the main load-bearing elements. The roof is made of carbon fibre, fabricated and then cured in a single session in the autoclave. Both areas use dual tubular bladders, an innovative production method derived from Formula 1. The tub and roof both use internal carbon-fibre and Rohacell/Nomex sandwich panels as load-bearing structures.
As on the LaFerrari, the sills act as side impact absorbers. The asymmetric layout of the cabin allowed each side of the tub to be optimised separately: the driver side has an adjustable seat, with a generous range of positions ensuring driving comfort and safety in the event of a side-on impact. This necessitated a larger number of structural panels in the floor and longer impact absorbers on the driver side than the passenger side, where a fixed seat is used to save weight while still ensuring uncompromised safety for both occupants.
The front aluminium impact-absorbing longerons also contribute to heat management, as their hollow interiors are used as cooling air ducts for the brake system. Ferrari co-developed a new casting solution that has reduced the minimum wall thickness limit previously applicable for these castings (2.0 mm) by 23%. Together, these solutions have brought a weight saving of 5% while increasing torsional and beam stiffness by 50% with respect to the LaFerrari. NVH has also been significantly improved to offer the most comfortable driving experience possible.
Bodyshell
The bodyshell of the F80 is completely new and is fabricated from pre-preg carbon fibreand cured in the autoclave using technology derived from Formula 1 and other motorsports. The front bonnet features an S-Duct consisting of a fixed element connecting the two front wings.
Butterfly doors are used, as on the LaFerrari, with a dual axis of rotation hinge mechanism allowing them to open vertically to an angle of almost 90°. The substructure of the doors, a structural element also tasked with absorbing dynamic loads in the event of lateral impact, is constructed from special high-performance carbon fibre.
The rear engine cover, which echoes the styling cues of the door from the side view, includes six slots venting hot air from the V6 engine and a grille which also vents air.
Design
Exterior
The 250 is the product of a creative design study that has led the team of the Ferrari Styling Centre headed by Flavio Manzoni to make a radical change in the visual language of the marque, forging a link between the past and future of Ferrari design. With the intent of assimilating a host of different elements of the design language and DNA of the brand, this study first turned its attention to the aesthetics of the marque’s F1 racing cars to identify the direction for creating a car with a modern and innovative visual identity that can accommodate a driver and a passenger despite offering the uncompromised experience of a single-seater.
With this logic as the foundation, the design of the F80 was then developed with technological input, lending the car its boldly high-tech character. The ambitious performance goals necessitated a holistic approach to the project; as a result, the formal design project for the F80 progressed from start to definitive completion with the Styling Centre working in constant synergy with the engineering, aerodynamics and ergonomics departments. From the very first sketches and the more abstract initial studies in form, the project evolved in a process of natural convergence to strike a perfect balance between form and volume that visually expresses the uncompromised performance of the car to perfection.
The F80 has a strongly futuristic visual impact with unmistakeable references to aerospace. The architecture is defined by a dihedral cross section with its two bottom corners firmly planted on the wheels. From the side view, the rear section has a sculpted flow that emphasises the muscularity of the entire rear wing. The front section of the car is defined by more architectural elements: the wheelarch ends with a vertical panel that stands proud of the door paying homage to the visual language of the F40.
Rising out from the volumes of the lower body is the cabin, a floating bubble structure of unexpected volumes, and the product of an exacting study in architecture and proportion. A whole 50 mm lower than greenhouse of the LaFerrari, the cab has a significant effect on the perception of volume, broadening the shoulders of the car to give the cockpit an even more compact look.
As on all latest-generation Ferraris, the contrast between the upper zone in bodywork colour and the lower zone in clear-coat finished carbon fibre accentuates the design of the car, revealing more of its technical side with each new glance. The designers wanted to avoid an anthropomorphic effect at the front of the F80; the headlamps are concealed in a visor element, a black screen serving both aerodynamic and lighting functions that gives the F80 a particularly original appearance.
The short-tail rear of the car has two different configurations during use: with the mobile wing stowed or deployed. The tail lights are set into a two-layer structure consisting of the tail fascia and the spoiler, creating a sandwich effect that gives the rear an extremely sporty character in both configurations.
With the rear spoiler raised, the car expresses even more power and dynamism as the difference in visual balance between the two configurations reveals the other side of its character. The functional needs of the car have been resolved visually in the design to create the perfect dialogue between performance and form. Some of these functional features play a very strong role in defining the visual character: the NACA duct channelling air towards the engine intake and lateral radiators, for example, is as iconic as it is functional, and constitutes one of the most original styling cues of the flank.
Another functional but highly symbolic element is the louvred engine compartment spine, where six slots, one for each cylinder of the internal combustion engine, create an unexpected relationship between the geometric lines and sculptural surfaces of the car.
Interior
The compact proportions of the cabin were made possible by opting for a cockpit inspired by a singleseat racer, creating a visual perception akin to an enclosed Formula 1 car. A lengthy process involving designers, engineers, ergonomics specialists and Colour & Trim experts culminated in an original new solution that sets the driver unequivocally as the protagonist in the cabin and transforms the car into a “1+”.
The decidedly enveloping cockpit is centred entirely around the driver, with its forms converging towards the controls and instrument panel. The control panel is also oriented ergonomically towards the driver, creating a sort of cocoon effect around them.
While ergonomically complete and comfortable, the passenger seat is so well integrated into the trim of the cabin that it almost disappears from view, a result also made possible by the masterful differentiation between the colours and materials used for the driver seat and for the rest of the trim.
A longitudinal offset in the positions of the seats of the two occupants made it possible to set the passenger seat farther back than the driver seat, allowing for a narrower interior space with no penalty in terms of ergonomics and perceived comfort. This solution let the designers give the car a smaller cabin and reduce the frontal cross section of the car.
The F80 also boasts a new steering wheel developed specifically for this car, which will make an appearance in the future road-going models of the Prancing Horse. Slightly smaller than its predecessor and with flattened top and bottom rims, the steering wheel also has a smaller boss, improving visibility and accentuating the sense of sportiness when driving. The lateral zones of the rim are optimised to ensure a better grip with or without gloves. The physical buttons on the right and left hand spokes of the steering wheel make a return here, replacing the full-digital layout used by Ferrari in recent years with a solution with easier to use buttons that can be instantly identified by touch.
7-year maintenance
Ferrari’s unparalleled quality standards and increasing focus on client service underpin the extended seven-year maintenance programme offered with the F80. Available across the entire Ferrari range, this is the first time this programme has been offered on a supercar and covers all regular maintenance for the first seven years of the car’s life. This scheduled maintenance programme for Ferraris is an exclusive service that allows clients the certainty that their car is being kept at peak performance and safety over the years. This very special service is also available to owners of preowned Ferraris.
Regular maintenance (at intervals of either 20,000 km or once a year with no mileage restrictions), original spares and meticulous checks by staff trained directly at the Ferrari Training Centre in Maranello using the most modern diagnostic tools are just some of the advantages of the Genuine Maintenance Programme. The service is available on all markets worldwide and from all Dealerships on the Official Dealership Network.
The Genuine Maintenance programme further extends the wide range of after-sales services offered by Ferrari to meet the needs of clients wishing to preserve the performance and excellence that are the signatures of all cars built in Maranello.